Industries - Quick Links:
Air Pollution Control Equipment
by Industry
Many types of air pollution control equipment are used across nearly all industrial processing and manufacturing industries to reduce emissions of volatile organic compounds (VOCs), hazardous air pollutants (HAPs), and other greenhouse gases (GHG).
Pollution control devices and abatement equipment are used in nearly every industrial processing and manufacturing industry.
Types of Industrial Pollution Equipment:
- Oxidizers
- Thermal Oxidizers
- Direct-fired
- Recuperative
- RegenerativeThermal Oxidizers
- Regenerative (RTO): Two-chamber
- Regenerative (RTO): Three-chamber
- Regenerative (RTO): Rotary
- Catalytic Oxidizers
- Direct-fired
- Recuperative
- Regenerative
How Much Should It Cost? Find a Supplier, Get a Quote.
Animal Feed Pollution Control
Applications / Use Cases
Animal feed manufacturing creates airborne particulates, dust, and odor pollution - resulting from the grinding, pelleting, and drying processes. The dust particles and odors generated are introduced into the exhaust stream and need to be captured and neutralized before they may be released to atmosphere.
Primary Contaminants
- Dust
- Particulates
- Odors
Types of Equipment Used
- Dust Collectors
- Recuperative Thermal Oxidizers - does not require pre-filtration in most cases.
- Regenerative Thermal Oxidizers
Key Challenges
The primary challenge in the animal feed industry is for larger plants with large exhaust air volumes. A large volume flow rate odor problem means we will need to use a Regenerative Thermal Oxidizer (RTO). The problem is that the ceramic media in the RTO has small gaps and is very prone to clogging easily. A comprehensive dust/particulate filtering solution will be required for the combined system to have a long life. Both wet and dry filter options are available.
Recommended Suppliers
Recommended Suppliers with Industry Experience:
- Catalytic Products
- Offers thermal oxidizers and dry filtration solutions Request a quote from Catalytic Products
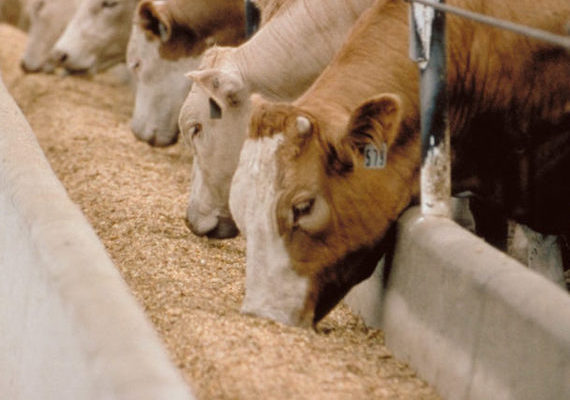
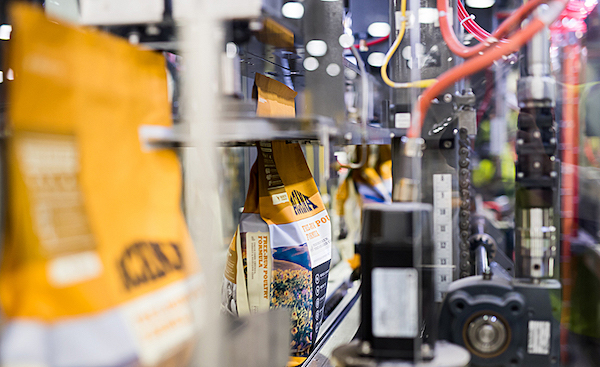
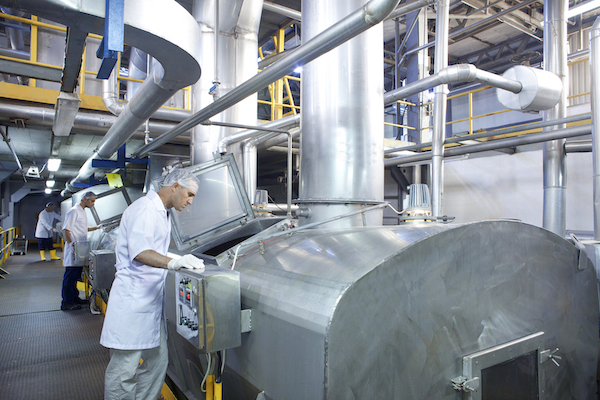
How Much Should It Cost? Find a Supplier, Get a Quote.
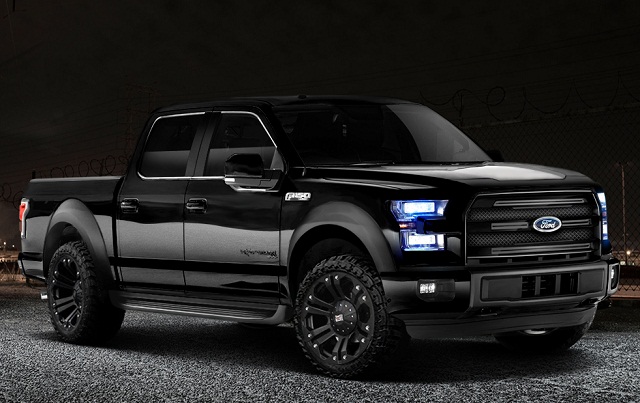
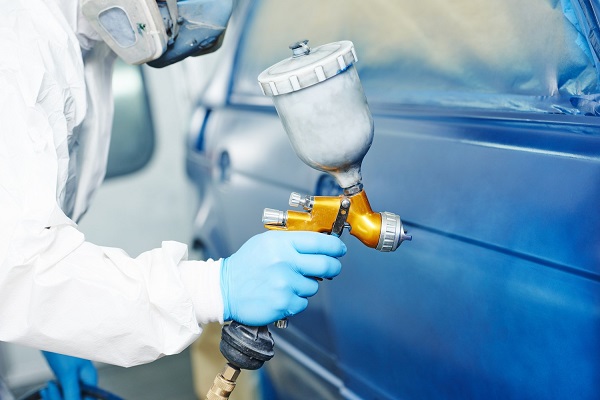

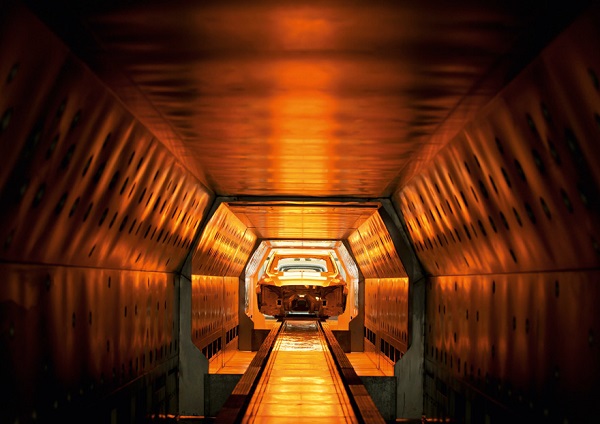
Automotive Industry Pollution Control
Applications / Use Cases
Air pollution control applications in the Auto industry include:
- Vehicle body painting applications, including paint booth and cure oven emissions,
- Plastic bumper/fascia and component painting,
- Engine test stations,
- Tire manufacturing, and
- Dashboard component coating.
Primary Contaminants
- VOCs - Volatile Organic Compounds
- HAPs - Hazardous Air Pollutants
- Odors
- Particulate from paint overspray
Types of Equipment Used
- Thermal Oxidizers - to treat paint solvent emissions from small paint lines
- Regenerative Thermal Oxidizers - to treat paint solvent emissions from large paint lines
- Catalytic Oxidizers - to treat engine emissions from QA test stands.
- Wet Scrubber - A wet scrubber is typically integrated directly into the paint booth itself and provided by the paint system equipment supplier.
Key Challenges
Recently, many automotive paint suppliers have started using siloxanes and silicon-based chemicals as a flow additive/agent and to promote cross-linking in the cured paint. These compounds provide unique challenges for RTOs and Adsorption systems alike. The siloxanes can be highly volatile, meaning they will vaporize and reach the pollution control equipment in gas phase. In the case of RTOs, the siloxanes will form silicone dioxide (SiO2) in the combustion chamber, coating the ceramic media with a highly-stable white powder that cannot be burned out or washed out. Typically, the upper layer of heat exchange media will need to be replaced periodically.
Recommended Suppliers
Recommended Suppliers with Industry Experience:
- Catalytic Products (CPI)
- Offers thermal oxidizers, catalytic oxidizers, concentrators, filtration systems, and heat exchangers. CPI has provided RTOs to Honda, Volkswagen, and more. Catalytic Products in the Automotive Industry
How Much Should It Cost? Find a Supplier, Get a Quote.
Building Materials Pollution Control
Applications / Use Cases
Sources of air pollution that are common to manufacturing of building materials include: dryers, ovens, furnaces, boilers, and kilns used for production of bricks, tiles, insulation, glass, cabinets, drywall, and roofing products can emit many pollutants simultaneously, often requiring multi-stage emission control. Batch mixing, cutting, buffing, polishing, and finishing processes often produce particulate matter, aerosols, and fine dust requiring efficient capture and filtration to reduce and eliminate health risks to plant workers and the surrounding community.
Specific applications, include:
- Glass production
- Vinyl manufacturing
- Fiberglass insulation
- Foam panels, boards, & cores
- Expanded Polystyrene (EPS) - Styrofoam
- Asphalt / Cement processing
- Asphalt roofing products
- Kitchen & bath fixtures
- Lighting products (bulbs & fixtures)
- Brick & tile production
- Ceramic products
- Textile production
- Wood products & laminates
- OSB / Engineered wood
- Flame lamination emissions
- Drywall & gypsum products
- Product safety testing oven emissions
Primary Contaminants
- Acid & alkaline gases & fumes – NH3, H2S, HCl, SO2, HF
- Alcohols
- Fine aerosols
- Particulate matter – PM10 & PM2.5
- Odors
- VOCs
- Mist & Dust Collection
- HAPs from Dryer & Oven exhaust
Types of Equipment Used
- Thermal Oxidizers - for destruction of VOCs and odors.
- Regenerative Thermal Oxidizers
Key Challenges
The primary challenge in the building materials industry is when multiple types of airborne contaminants are present requiring multiple stages of emission capture, such as a wet scrubber with a thermal oxidizer or dust collector and carbon adsorber. Often times, multiple stages of capture may be required.
Recommended Suppliers
Recommended Suppliers with Industry Experience:
- Catalytic Products (CPI)
- Offers thermal oxidizers, catalytic oxidizers, concentrators, filtration systems, and heat exchangers. CPI has provided RTOs to multiple Fortune 500 companies. Request a quote from Catalytic Products
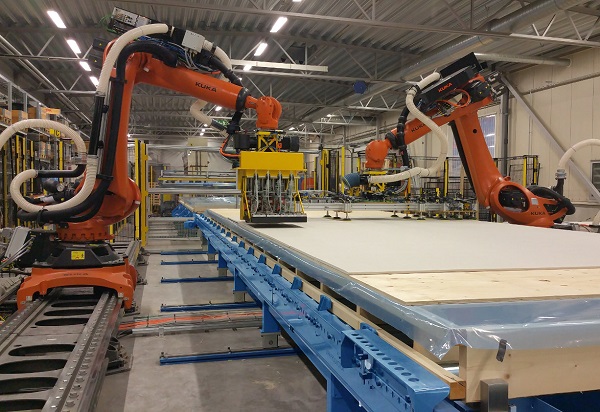
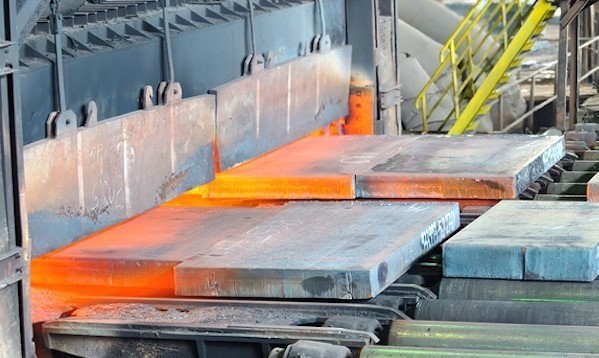
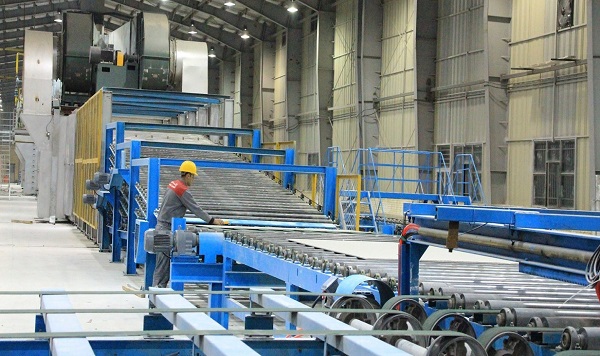
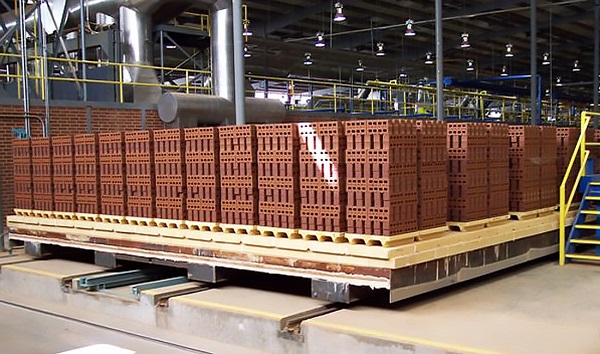
How Much Should It Cost? Find a Supplier, Get a Quote.
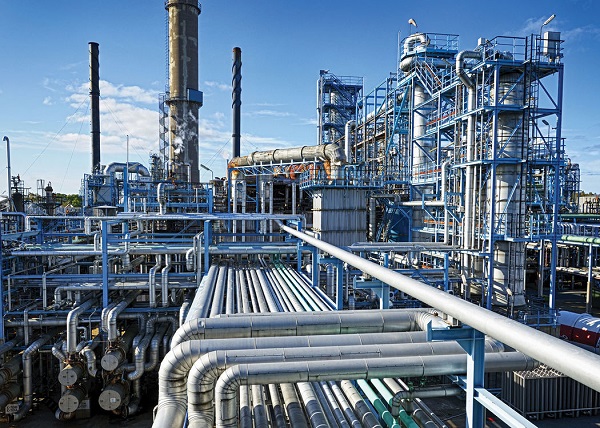
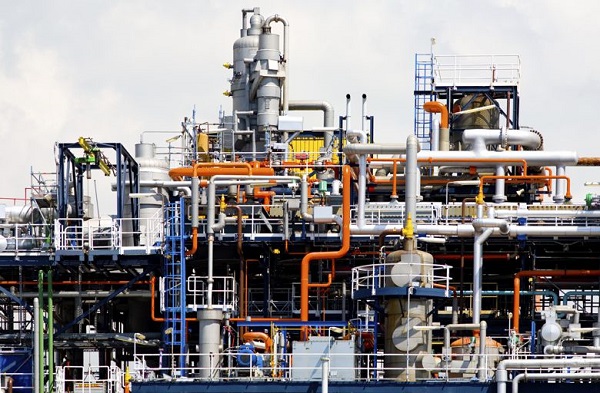
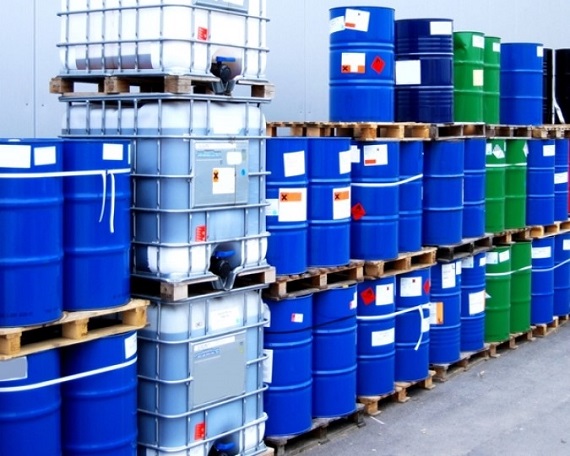
Chemical Industry Pollution Control
Applications / Use Cases
Air pollution control applications in the Chemical industry include:
- Acid production
- Ethanol, Corn Processing, Biodiesel
- Fertilizer plants
- Halogenated compounds (Fl, Cl, Br, etc)
- Toxic chemicals and gases
- Specialty chemicals
- Formaldehyde
- Petrochemicals
- Aromatic hydrocarbons
- Ammonia
- Adhesives
- Flavors and Fragrances
- Paint and coatings production
Primary Contaminants
- VOCs - Volatile Organic Compounds
- HAPs - Hazardous Air Pollutants
- Odors
- Toxic chemicals and gases
Types of Equipment Used
- Thermal Oxidizers - to treat VOCs and other organic chemical gas emissions.
- Regenerative Thermal Oxidizers
- Catalytic Oxidizers - to treat pure chemical emissions from a single process.
Key Challenges
Chemical processing can be done in a batch or a continuous process, which provides an additional challenge for managing VOC loading and staying under 25% LEL levels.
Chemical production also produces some corrosive and other toxic inorganics that require scrubbing prior to oxidation. Multiple systems in series are common to handle all the contaminants.
Recommended Suppliers
Recommended Suppliers with Chemical Industry Experience:
Oxidizer Suppliers:
- Catalytic Products (CPI)
- Offers thermal oxidizers, catalytic oxidizers, concentrators, filtration systems, and heat exchangers. CPI has provided equipment to ICL Specialty Fertilizers, Lithographic Industries, BE&K, GreenMantra Tech, and Advanced FlexComp. Catalytic Products in the Chemical Industry
How Much Should It Cost? Find a Supplier, Get a Quote.
Coatings Industry Pollution Control
Applications / Use Cases
Air pollution control applications in the Coatings industry include spraying or applying paints, coatings, laminates, or solvents, and the curing ovens for those coatings. Specific applications include:
- Coil coating
- Wire coating
- Plastics
- Aluminum cans
- Paper
- Magnetic tape
- Parts coating
- Metal components
- Drum coating
- Flow coating
- Fasteners coating
- Coatings manufacturers / coatings suppliers
Primary Contaminants
- VOCs
- Hydrocarbons
- Aromatic hydrocarbons
- Ketones
- Xylenes
- Hexane
- Ethers
- Odors
- Toxic fumes, such as isocyanates
Types of Equipment Used
- Thermal Oxidizers - effective at destroying VOCs, odors, and some toxic fumes.
- Regenerative Thermal Oxidizers
Key Challenges
For a coating process, the key pollution control challenges include installing a permanent total enclosure (PTE) to capture fugitive emissions and recycling, recirculating, or cascading exhaust air to reduce the total volume of exhaust air sent to abatement. All strategies seek to increase capture efficiency while reducing air volume, thereby concentrating the VOCs in the process exhaust air.
Recommended Suppliers
Recommended Suppliers with Coating Industry Experience:
Oxidizer Suppliers:
- Catalytic Products (CPI)
- Offers thermal oxidizers, catalytic oxidizers, concentrators, filtration systems, and heat exchangers. CPI has provided equipment to Lithographic Industries, BE&K, GreenMantra Tech, and Advanced FlexComp. Catalytic Products in the Coatings Industry
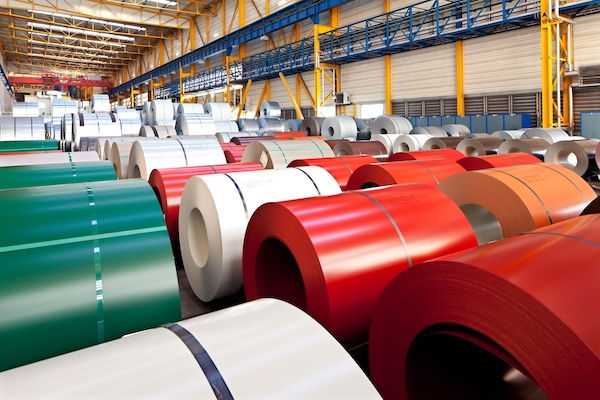
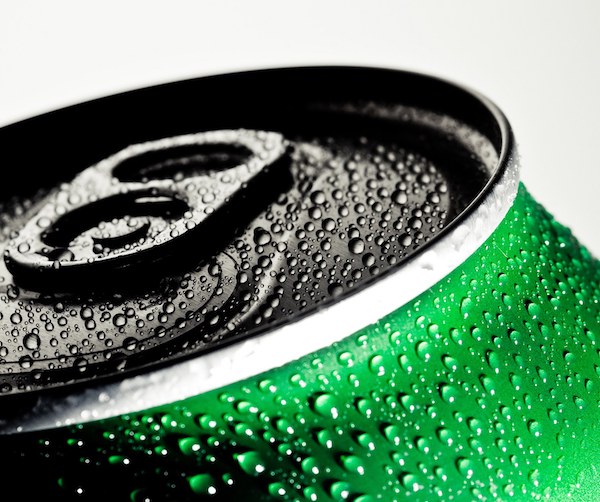
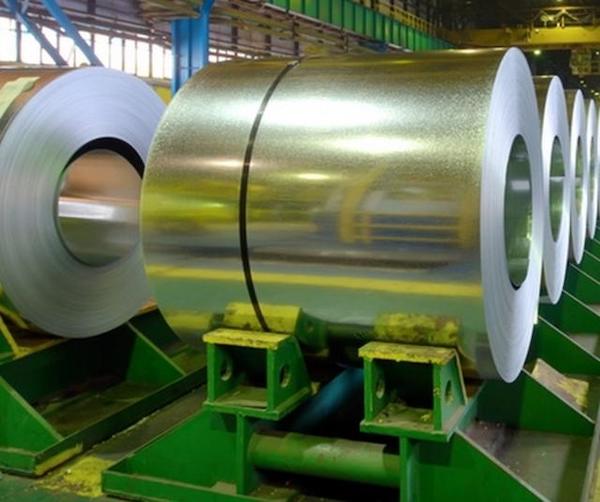
How Much Should It Cost? Find a Supplier, Get a Quote.

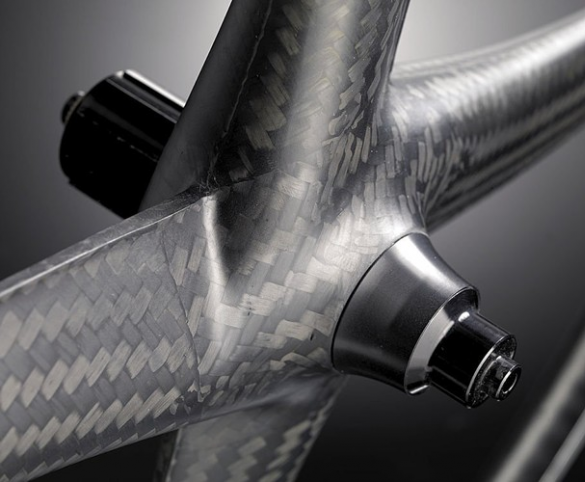
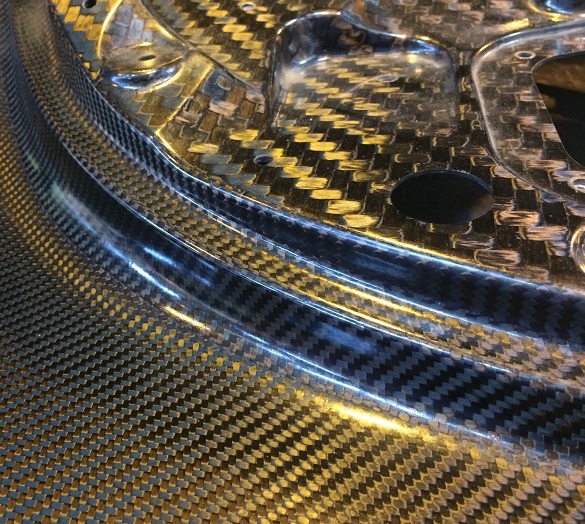
Composites Industry Pollution Control
Applications / Use Cases
Air pollution control applications in the Composites industry include:
- Carbon Fiber furnace and oven emissions
- Low- and High-Temperature (LT / HT) furnaces
- Fiberglass Polymer emissions
- Fiber Reinforced Plastic (FRP) production
- Fiber Web Resin Impregnation
- Styrene resin emissions
- Spraying clearcoat and other coatings
- Composite Parts Coating Cure Ovens
Primary Contaminants
- VOCs - Volatile Organic Compounds
- Styrene
- Xylene, Ethyl Benzene, and Phenol
- HAPs - Hazardous Air Pollutants
- Hydrogen Cyanide (HCN)
- Ammonia (NH3)
- Silicon Dioxide (SiO2)
- Nitrous Oxide (NOX)
- Carbon Monoxide (CO)
- Tar
- Odors
Types of Equipment Used
- Direct-fired Thermal Oxidizers (DFTOs) - to treat high concentrations of styrene and other VOCs.
- Regenerative Thermal Oxidizers - to abate large volumes of VOCs and HAPs.
- Catalytic Oxidizers - when the chemical formula is simple and stable, a CATOX system may be used to reduce energy costs.
Key Challenges
Due to the batch process, when composite parts are loaded into the furnace, it causes a large burst of VOCs and HAPs to be released in a narrow window of time. The oxidation equipment needs to be able to handle large variations in VOC loading during production.
Another challenge is styrene emissions. High styrene content is key to product quality and longevity, but capturing and destroying styrene emissions can be expensive. Balancing the quality and production cost equation can be tricky.
Recommended Suppliers
Recommended Suppliers with Industry Experience:
- Catalytic Products (CPI)
- Offers thermal oxidizers, catalytic oxidizers, concentrators, filtration systems, and heat exchangers. CPI has provided equipment to Advanced Flexible Composites. Catalytic Products in the Composites Industry
How Much Should It Cost? Find a Supplier, Get a Quote.
Food Processing Pollution Control
Applications / Use Cases
The food and beverage industries use various cooking and processing methods that create hazardous and/or odorous emissions:
- Food processing
- Beverage production
- Bakery ovens - Ethanol
- Brewery
- Meat cookers
- Fish, fishmeal, & fish oil
- Cheese
- Roasting
- Oven
- Frying
- Rendering animal fats
- Candy/Confectionery Panning/Polishing/Glazing
- Coffee & Cocoa Bean Roasting
- Flavoring, spices, and aromatics
- Particulate from coffee roasting
- Grease from frying and rendering operations
- Smoke emissions
- Gum manufacturing
- Other sticky or volatile vent streams
Primary Contaminants
- Grease / Oil Mists
- Particulates / Flour Dust
- Odors
- Hazardous Air Pollutants (HAPs):
- Hydrogen Sulfide (H2S)
- Ammonia (NH3)
- Mercaptans / Thiols (-SH)
- Sulfur Dioxide (SO2)
- Hydrochloric Acid (HCl)
- Acetic Acid (CH3COOH)
- Phosphoric Acid (H3PO4)
- Volatile Organic Compounds (VOCs)
- Ethanol
- Other alcohols, esters and aldehydes
- Opacity
Types of Equipment Used
Key Challenges
In the food industry, high levels of humidity are often found in the exhaust streams from the various cooking processes. This humidity and heat can cause corrosion issues in the ductwork and air pollution abatement equipment, so typically stainless steel components and ductwork will be used.
When dealing with high levels of grease, oil, and particulate - filtration is typically required. Options include fabric filters, cartridge filters, wet scrubbers, self-cleaning ceramic filter (SCCF).
If using an RTO for ethanol, for example, the various particulates must be filtered out prior to the RTO or they will clog the media.
Recommended Suppliers
Recommended Suppliers with Food Industry Experience:
Oxidizer Suppliers:
- Catalytic Products (CPI)
- Offers thermal oxidizers, catalytic oxidizers, concentrators, filtration systems, and heat exchangers. CPI has provided equipment to multiple confectioners, multiple flavorings plants, a Southern USA bakery, and an Eastern US Bakery. Food & Bakery experience from Catalytic Products

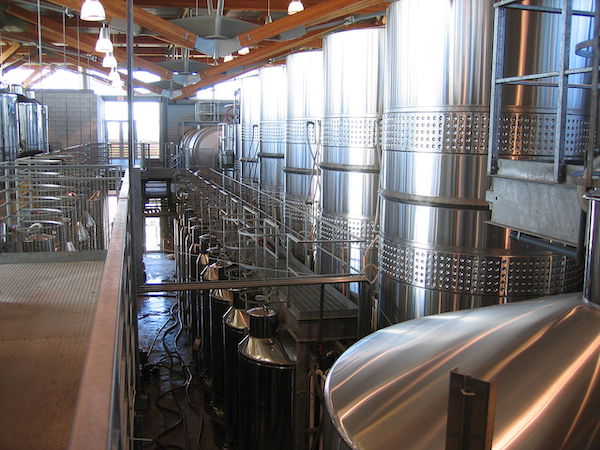
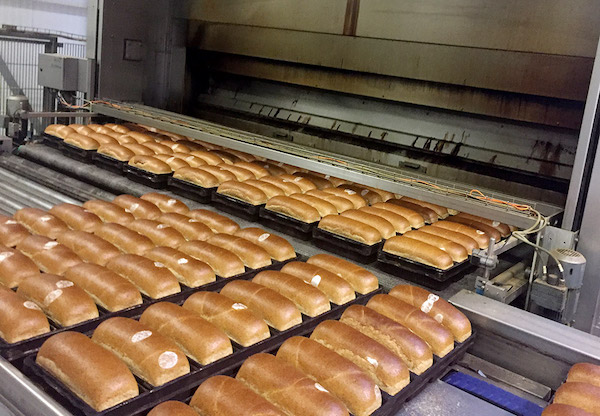
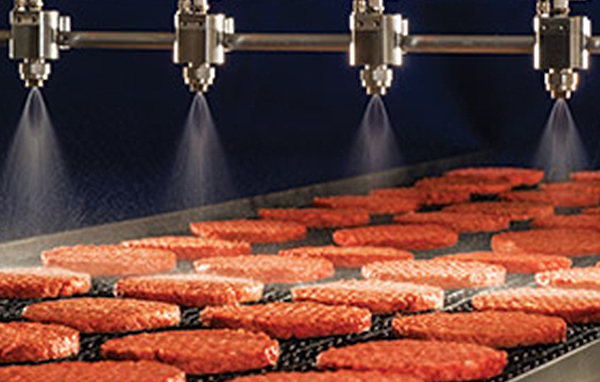
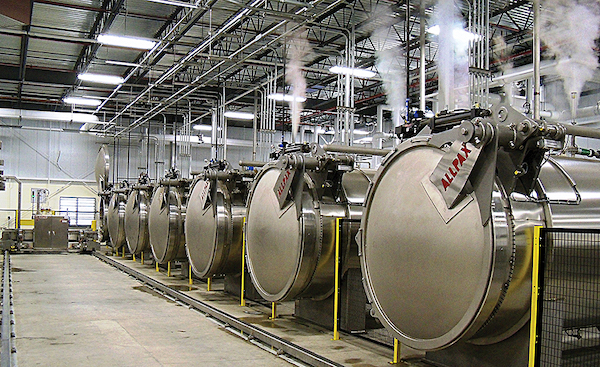
How Much Should It Cost? Find a Supplier, Get a Quote.
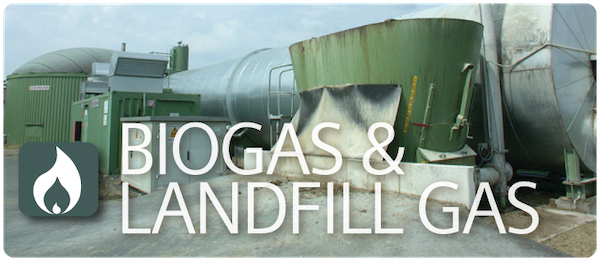
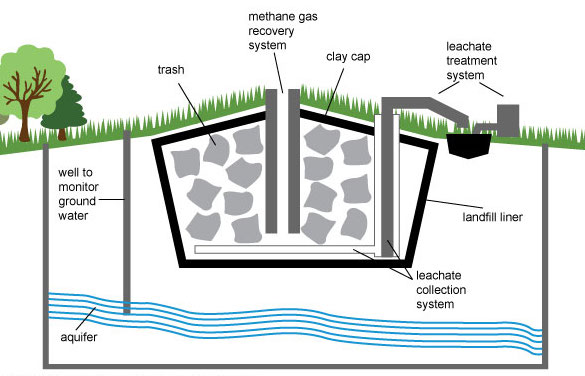
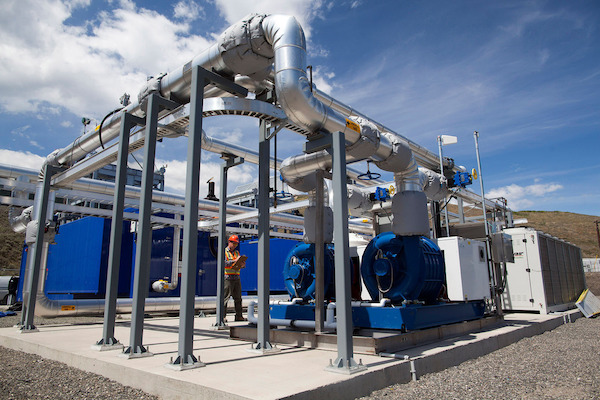
Landfill & Biogas Pollution Control
Applications / Use Cases
Air pollution control applications include:
- Landfill off-gas: Landfills are the single largest source of U.S. man-made methane emissions.
- Municipal solid waste landfill (MSWLF)
- Biogas - produced by the anaerobic decomposition or breakdown of organic matter in the absence of oxygen.
- Decomposition of agricultural waste, manure, municipal waste, plant material, sewage, green waste or food waste.
- Volatilization of organic compounds
- Other renewable energy processes
Primary Contaminants
- VOCs - Volatile Organic Compounds
- Methane
- NMOC - Nonmethane Organic Compounds
- Odors
- Hydrogen Sulfide - H2S - distinct rotten-egg odor
Types of Equipment Used
- Direct-fired Thermal Oxidizer - if the landfill gas or biogas is 3-5% methane by volume or greater, then a DFTO can operate in a steady-state condition without supplemental natural gas. If biogas is 1.5-3% by methane, a Thermal Recuperative Oxidizer (TRO) with 60% heat exchanger may be used for steady-state operation.
- Regenerative Thermal Oxidizers - To treat biogas when the methane concentration is less than 1.5% by volume.
Background Info
Most landfill gas is produced by bacterial decomposition, which occurs when organic waste is broken down by bacteria naturally present in the waste and in the soil used to cover the landfill. Organic wastes include food, garden waste, street sweepings, textiles, and wood and paper products. Peak production of methane and biogas occurs after the waste has been buried for 5-7 years. The rate of biogas production depends on amount of oxygen present, moisture content, temperature, and age of landfill.
Recommended Suppliers
Recommended Suppliers with Industry Experience:
- Catalytic Products (CPI)
- Offers thermal oxidizers, catalytic oxidizers, RTOs, and heat exchangers. CPI has provided equipment to landfills for waste gas abatement and to a Biogas Anaerobic Digestor operation for emissions control. Landfill experience from Catalytic Products
Renewable Fuels experience from Catalytic Products
How Much Should It Cost? Find a Supplier, Get a Quote.
Metal Finishing Pollution Control
Applications / Use Cases
- Metal Decorating
- Grinding and Drilling
- Polishing
- Coating and Laminating
- Galvanizing or Aluminizing
- CNC Machining
- Cleaning
- Shot Peening
- Chemical Milling
- Chemical Stripping
- Anodizing
- Electroplating
- Acid Etching
- Plating: Zinc, Nickel, Cadmium, Chrome
- Phosphating
- Aluminum bright dip
- Stainless steel and alloy pickling
- Coating application lines, flash-off areas, and drying/curing ovens
- Foundries: Aluminum, Cast Iron
- Mining and Minerals Processing, Quarries
- Precious Metal Recovery, Liquid Toluene
Primary Contaminants
Common emissions from the metal processing and finishing industry include:
- Metal dust and particulates
- VOCs - Volatile Organic Compounds
- Hazardous Air Pollutants (HAPs):
- Ammonia (NH3)
- Hydrochloric Acid (HCl)
- Nitric Acid (HNO3)
- Sulfuric Acid (H2SO4)
- Chromic Acid
- Hydrofluoric Acid (HF)
- Phosphoric Acid
- Alkaline emissions, Sodium Hydroxide (NaOH)
- NOx gases, such as NO and NO2
Recommended Suppliers
Recommended Suppliers with Metal Finishing Industry Experience:
Oxidizer Suppliers:
- Catalytic Products (CPI)
- CPI offers RTOs, thermal oxidizers, catalytic oxidizers, RCOs, as well as filtration systems and heat exchangers. Metal decorating emissions control with CPI
Industry experience & Case studies
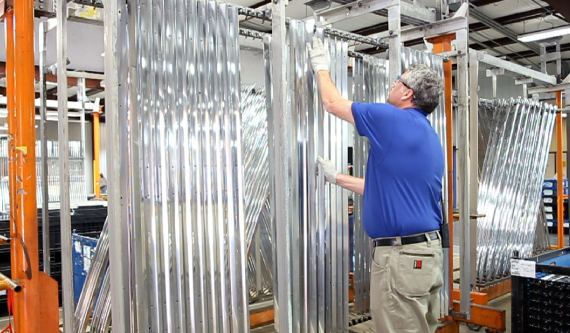
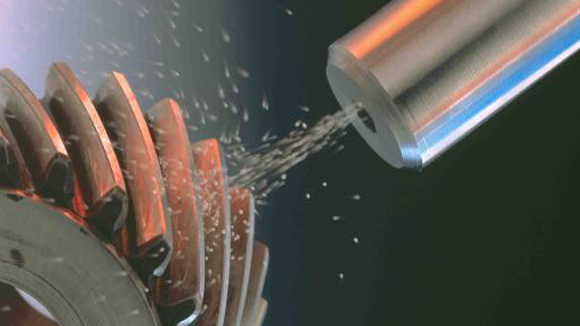
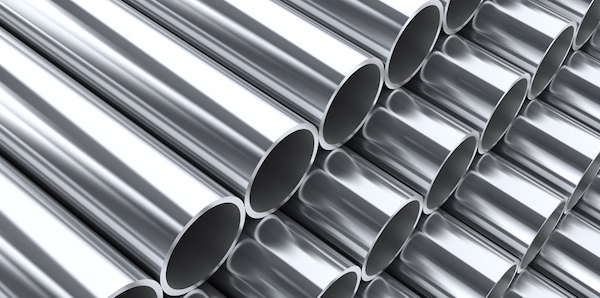
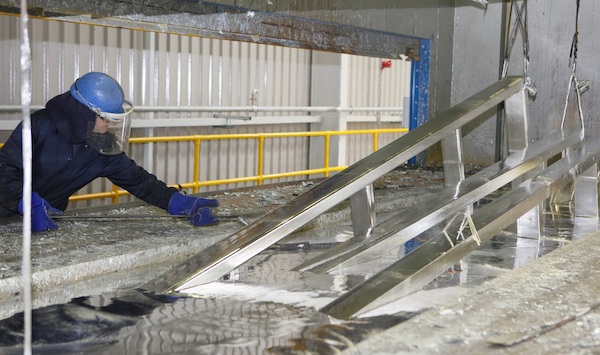
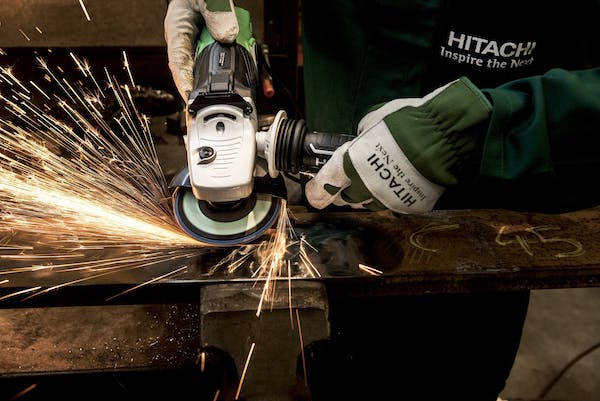
How Much Should It Cost? Find a Supplier, Get a Quote.
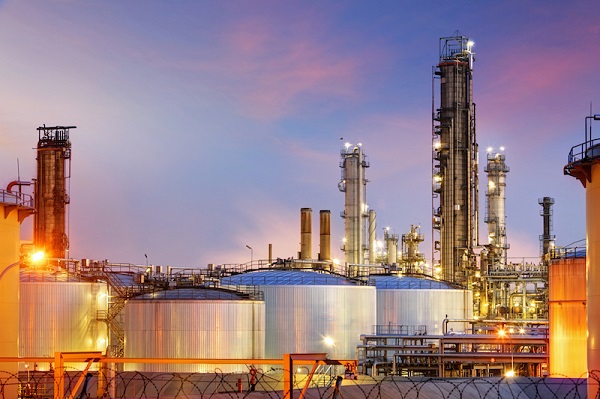
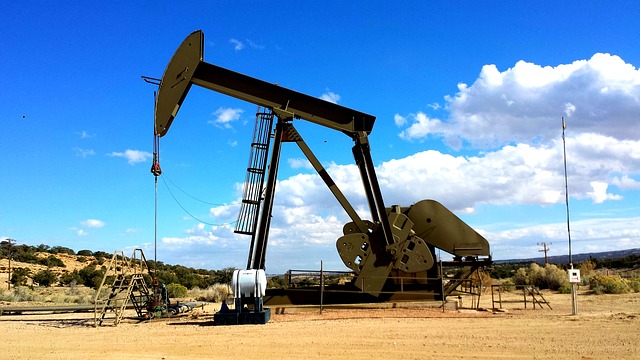
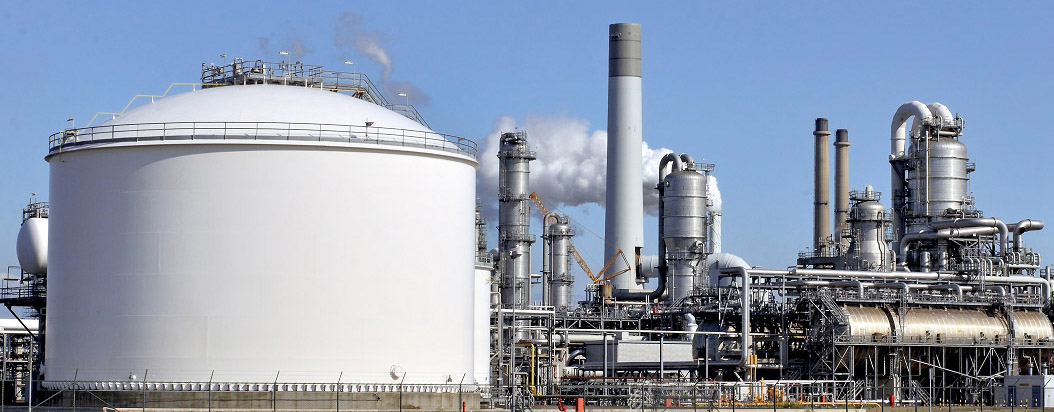
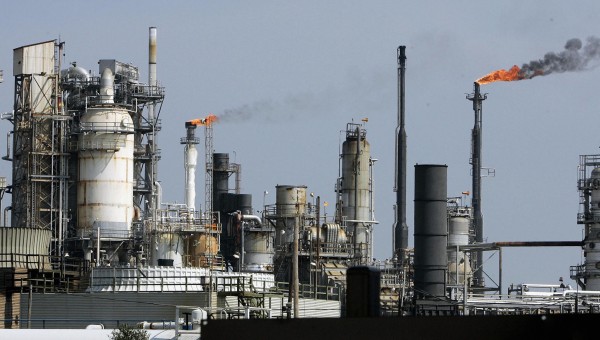
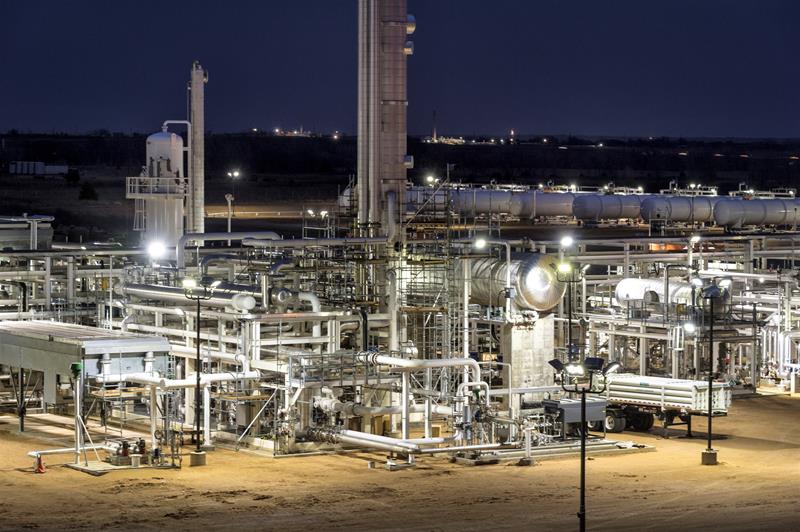
Oil & Gas Industry Pollution Control
Applications / Use Cases
Air pollution control applications in the Oil & Gas industry include:
- Tail gas emissions
- Off-gas treatment
- Petroleum refining
- Natural gas processing, transmission
- Tank venting
- Separators
- Sulfur recovery systems
- Wet wells
- Loading and unloading tank trucks
- Barge loading and unloading
- Liquefied Natural Gas (LNG)
- Amine stripper off gas (tail gas)
- Natural gas midstream facilities
- Natural gas fractionation plants
- Petrochemical plants
- Glycol dehydration
- Amine desulfurization / sweetening
- Refinery wastewater treatment
Primary Contaminants
- VOCs - Volatile Organic Compounds
- Methane
- Hydrocarbons: methane, ethane, propane, butane, benzene, etc.
- Petroleum by-products
- HAPs - Hazardous Air Pollutants
- Acid gases
- Odors
- Hydrogen Sulfide - H2S (sour gas) - rotten-egg odor
- Particulates
Types of Equipment Used
Equipment Restrictions
Catalytic oxidizers typically cannot be used because sulfur will poison/foul the catalyst material.
Recommended Suppliers
Recommended Suppliers with Industry Experience:
- Catalytic Products International (CPI)
- Offers thermal oxidizers, thermal combustion systems, and heat exchangers. CPI has provided RTOs other equipment to multiple Natural Gas Midstream Processing facilities. Oil & Gas industry experience from CPI
How Much Should It Cost? Find a Supplier, Get a Quote.
Packaging & Labeling Pollution Control
Applications / Use Cases
- Packaging and Labeling
- Flexible (Plastic) Packaging
- Plastic Bottles
- Folding carton
- Corrugated cardboard outer packaging
- Metal packaging, cans and boxes
- Aluminum cans, tin cans
- Light metal containers
- Closures and components
- Graphics application
- Metal lithography
- Drying ovens
- Metal decorating
- Food packaging, i.e. potato chip bags
- Labels and tapes
- Web Coating & Converting
Primary Contaminants
- VOCs - Volatile Organic Compounds
- Vapors from ink solvents, graphics, and laminates
- HAPs - Hazardous Air Pollutants
- Odors
Types of Equipment Used
- Recuperative Thermal Oxidizers - does not require filtration in most cases.
- Regenerative Thermal Oxidizers
- VOC Concentrator
Key Challenges
The primary challenge for air pollution control in the packaging and graphics industry is the capture of fugitive emissions and potential requirement of a Permanent Total Enclosure (PTE).
Recommended Suppliers
Recommended Suppliers with Industry Experience:
- Catalytic Products (CPI)
- Offers thermal oxidizers, catalytic oxidizers, concentrators, filtration systems, and heat exchangers. CPI has provided equipment to Celanese, Total, Dupont, Targa, 3M, and Honda. Request a quote from Catalytic Products
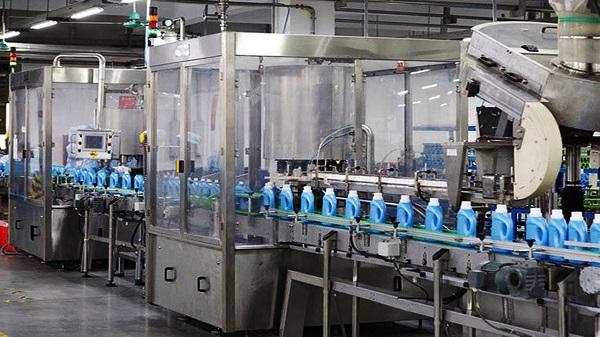
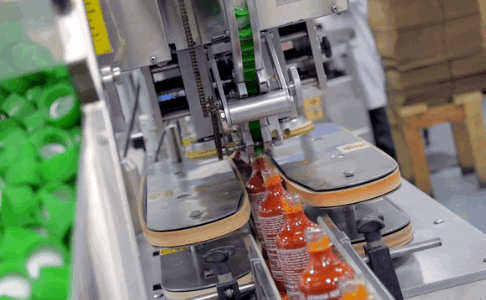
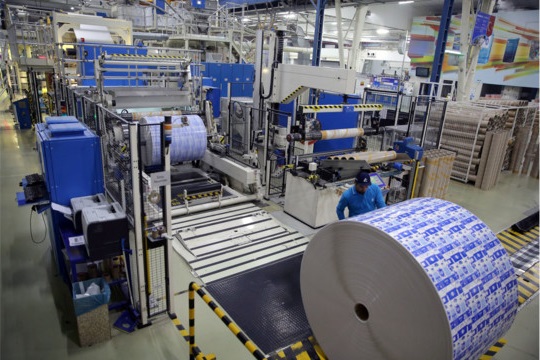
How Much Should It Cost? Find a Supplier, Get a Quote.
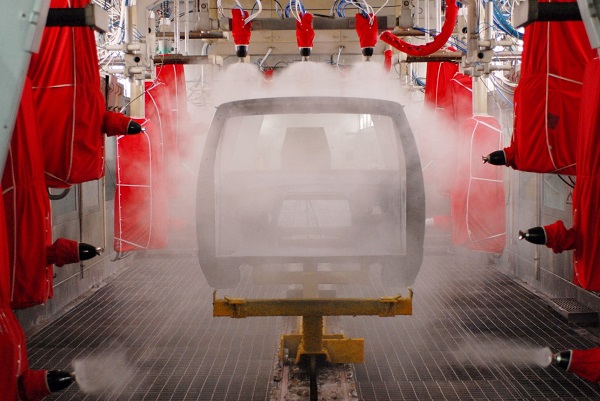
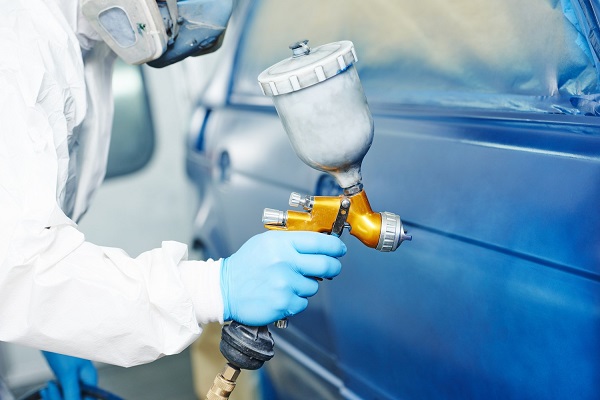
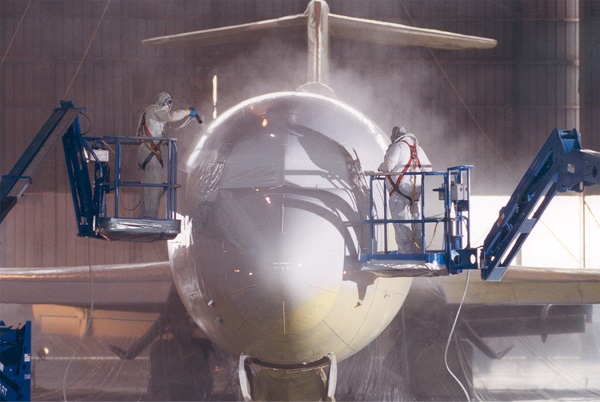
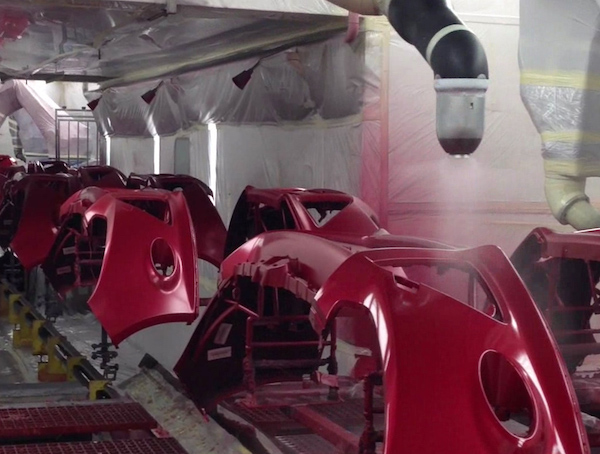
Painting Industry Pollution Control
Applications / Use Cases
Air pollution control applications for painting include:
- Paint spray booth exhaust
- Paint cure oven exhaust
- Heated or ambient flash-off tunnels
- Aerospace: Aircraft fuselages and parts
- Automotive: Vehicle bodies (metal), plastic bumpers
- Defense: Tanks, vehicles, missiles/weapons
- Semi-trucks and trailers
- Heavy machinery, construction equipment, cranes
- Off-road vehicles: 4-wheelers, ATVs, SxS, UTVs
- Bus painting
- Recreational vehicles (RVs)
- Rail car or train car painting
- Metal drum painting
- Plastic parts / component painting
- Paint mix room vents, tank vents
- Paint manufacturers / paint suppliers
Primary Contaminants
- VOCs - Volatile Organic Compounds
- Xylenes
- n-Butyl Acetate
- Heavy Naptha
- Alcohols, glycol ethers, ketones, esters
- Aromatic hydrocarbons
- Aliphatic hydrocarbons
- HAPs - Hazardous Air Pollutants
- Odors
- Toxic fumes, such as Isocyanate
- Particulate from paint over spray
Types of Equipment Used
- Regenerative Thermal Oxidizer - used to treat VOC emissions from a majority of paint booths, ovens, and other paint systems.
- Catalytic Oxidizers are not recommended due to the catalyst's sensitivity to paint formulation changes. Any future paint additives may foul the catalyst.
Key Challenges
- Exhaust air volume reduction via recycling
- Filtration of paint overspray and particulates
- If no booth, use of emissions-capture hoods and enclosures
- Siloxanes and silicon-based paint additives:
Recommended Suppliers
Recommended Suppliers with Paint Industry Experience:
- Catalytic Products (CPI)
- Offers thermal oxidizers, concentrators, filtration systems, and heat exchangers. CPI has provided RTOs to Honda, Volkswagen, Subaru, TKS, and more. Learn more from Catalytic Products
How Much Should It Cost? Find a Supplier, Get a Quote.
Pharmaceutical Air Pollution Control
Applications / Use Cases
Air pollution control applications for the Pharmaceutical industry include:
- Pill coating (tablet coating)
- Pill drying ovens
- Process reactor venting
- Mixing operations
- Distillation units
- Centrifuges
- Fluid-bed processing
- Tray drying
- Storage tanks
- Gas cylinder emergency release
- Biologics, biotechnology
- Bagging, bottling, dry mixing
- Vitamins, nutritional supplements
- Cosmetics, perfumes, toiletries
- Medical devices
- Disinfecting operation
- Ethylene Oxide (EtO) for medical equipment sterilization
Primary Contaminants
- VOCs - Volatile Organic Compounds
- Ethanol
- Isopropyl alcohol (IPA)
- Toluene
- Many organic solvents
- HAPs - Hazardous Air Pollutants
- Ethylene oxide (EtO)
- NOx
- Halogenated compounds - Chlorine, Fluorine, Bromine, etc.
- Hydrogen Chloride, Methylene Chloride
- Inert process streams
- Inorganic acids
- Nitric Acid
- Dust/Particulate
Types of Equipment Used
Oxidizers:
- Regenerative Thermal Oxidizer (RTO)
- Thermal Recuperative Oxidizer (TRO) and Direct-fired Thermal Oxidizers
- Catalytic Oxidizer (CATOX) - can be used to control ethylene oxide (EtO) and other processes with stable formulations.
Key Challenges
The primary challenge in the pharmaceutical industry is being able to handle both batch and continuous operations with the same VOC control equipment.
When processing in batches the exhaust volumes and VOC concentrations can be highly variable, from near-zero up to VOC concentrations in excess of 100% of LEL (lower explosion limit). Special care must be taken to dilute these exhaust gases to a safe, non-explosive concentration before sending to the oxidizer. The same VOC control equipment must also be able to handle high air volumes and lower VOC concentrations during purge periods between batches.
Other challenges include corrosive acids may be produced in the process off-gas or in the post-combustion gases. An acid gas scrubber must be used in combination with an oxidizer.
Recommended Suppliers
Recommended suppliers with Pharmaceutical industry experience:
Oxidizer and Scrubber suppliers:
- Catalytic Products (CPI)
- Offers thermal oxidizers, RTOs, catalytic oxidizers, and dry filtration solutions. CPI also offers a quench and scrubber add-on system for corrosive and acid gases. CPI has provided equipment to Mayne Pharma and a Fortune 100 Pharmaceutical manufacturer. Pharma & Medical at Catalytic Products
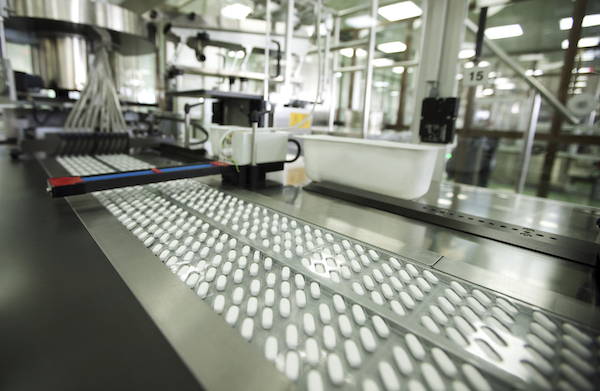


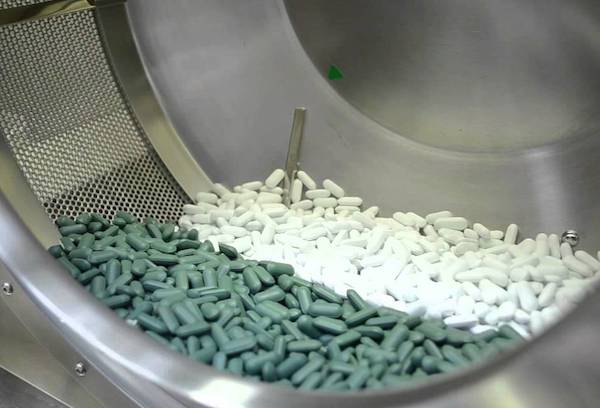
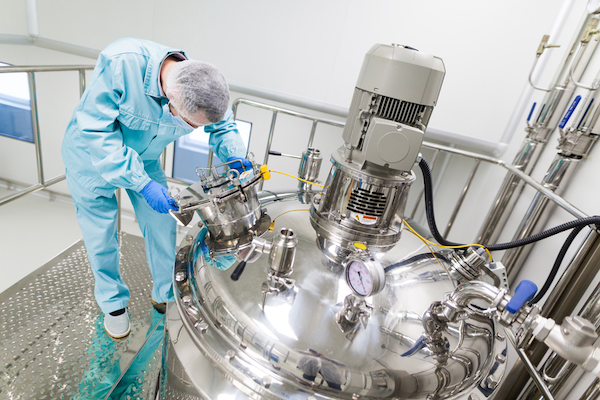
How Much Should It Cost? Find a Supplier, Get a Quote.
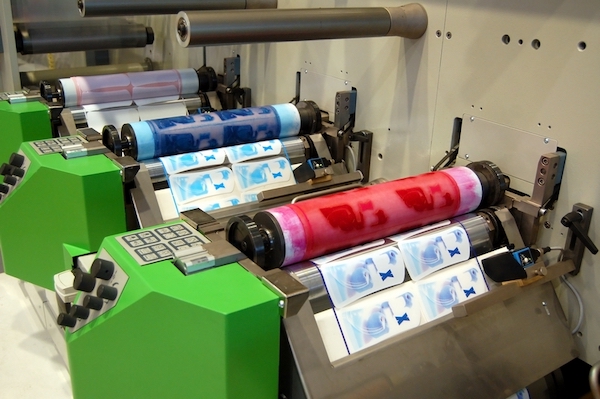
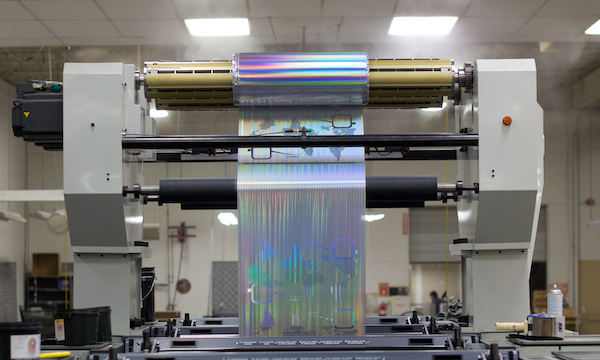
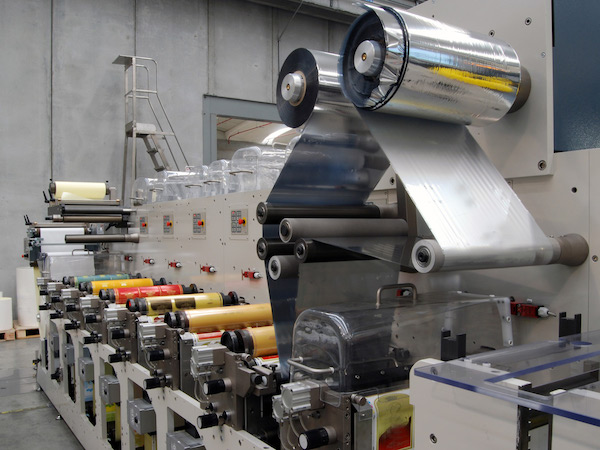
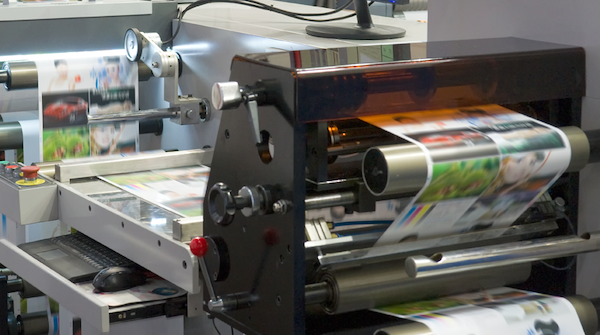
Printing Industry Pollution Control
Applications / Use Cases
Air pollution control applications in the Printing industry include:
- Flexographic printing (Flexography)
- Lithographic printing
- Gravure printing, Rotogravure
- Digital printing: inkjet & xerography
- Laser printing
- Offset lithography
- Newspaper publishing and printing
- Screen printing
- T-shirt, textiles printing
- Commercial printing
- Letterpress
- Ink manufacturing
- Web handling
- Print dryers
Primary Contaminants
- VOCs - Volatile Organic Compounds
- HAPs - Hazardous Air Pollutants
- Odors
- Toxic fumes
Types of Equipment Used
- Thermal Oxidizers - to treat print solvent emissions from small lines.
- Regenerative Thermal Oxidizers - to treat print solvent emissions from larger print lines.
- Catalytic Oxidizers
- VOC Concentrator
Key Challenges
Key challenges in the printing industry include capture of emissions, odors, and toxic fumes in the printing/press rooms and in the print dryers and ovens. Capture of all fugitive emissions may require an enclosure with negative pressure and exhaust fan. Consideration of water-based vs solvent-based inks is also important in designing a custom air pollution control system.
Before selecting equipment, customers should minimize the total exhaust air volume from printing operations by recirculating, recycling, or cascading air from low concentration and low temperature areas to areas of higher temperature and higher concentration before exhausting and sending to the final air pollution abatement device. This air volume reduction strategy will reduce the size of your oxidizer, saving you money in capital and operating costs.
Recommended Suppliers
Recommended Suppliers with Printing Industry Experience:
- Catalytic Products (CPI)
- Offers thermal oxidizers, RTOs, catalytic oxidizers, and dry filtration solutions. CPI also offers solutions for flexographic printing applications. Printing industry experience at Catalytic Products
How Much Should It Cost? Find a Supplier, Get a Quote.
Rubber & Plastics Pollution Control
Applications / Use Cases
Air pollution control applications in the Rubber & Plastics industries include:
- Rubber mixing
- Rubber curing / vulcanizing
- Natural or synthetic rubber
- Rubber products: tires, boots, hosing, belts, gaskets, seals, protective clothing
- Plastic injection molding
- Plastic products: plastic sheet, plastic pipe, plastic bottles
- Latex products
- Silicone rubber
- Styrene butadiene rubber (SBR)
- EPDM rubber
- Polychloroprene (neoprene rubber)
- Elastomers
- Cure oven exhausts
Primary Contaminants
- Blue haze
- Particulates / opacity
- VOCs - Volatile Organic Compounds
- Ethanol - from mixing
- HAPs - Hazardous Air Pollutants
- Odors
- Toxic fumes
Types of Equipment Used
- Regenerative Thermal Oxidizer - The RTO is a good fit for rubber manufacturing due to the low concentration of VOCs in the exhaust.
- Recuperative Thermal Oxidizers
Key Challenges
The primary challenge in the rubber and plastics industry is particulate carryover. The rubber manufacturing process releases sticky particulates that are tricky to transport. Minimizing duct runs is critical because the sticky particulates will build up can cause duct fires or thermal events. Typically a baghouse or wet dust collector is used prior to the oxidizer or prior to any long duct runs. Monitoring the baghouse for blow-outs is key to minimize the particulate build-up on critical surfaces, like ceramic media.
Recommended Suppliers
Recommended Suppliers with Rubber & Plastics Industry Experience:
- Catalytic Products (CPI)
- Offers thermal oxidizers, RTOs, catalytic oxidizers, VOC concentrators, and many filtration solutions. CPI also offers heat exchangers and heat recovery systems. CPI has provided equipment to Celanese, Total, Dupont, 3M, and Honda. Request a quote from Catalytic Products
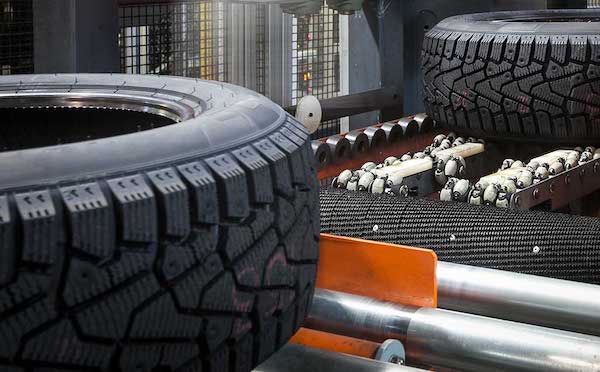
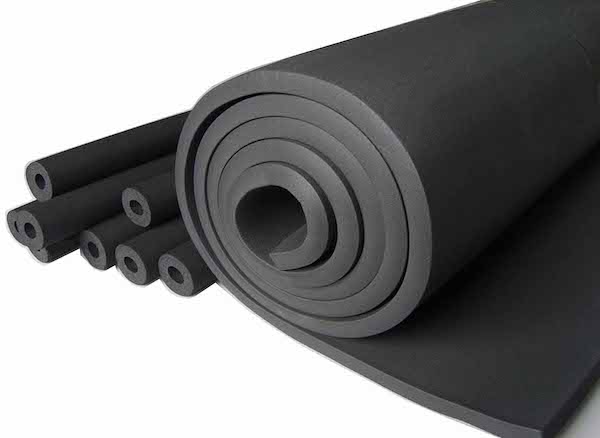
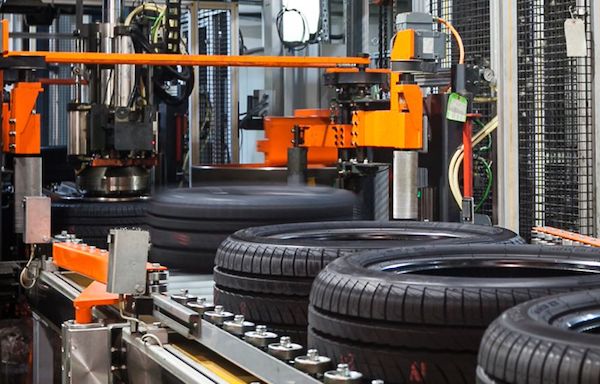
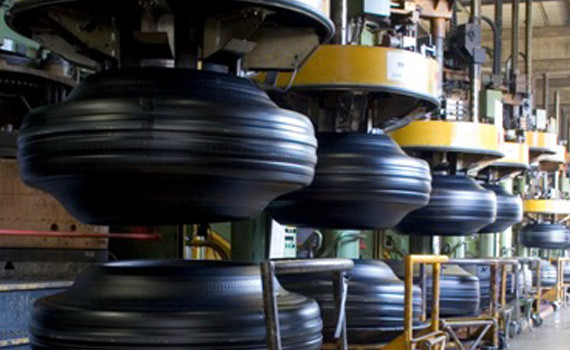
How Much Should It Cost? Find a Supplier, Get a Quote.
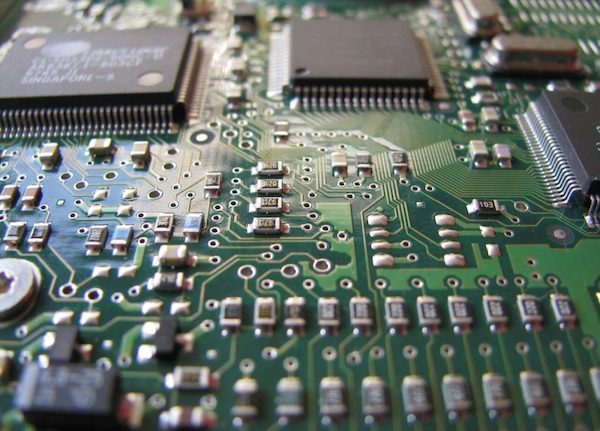
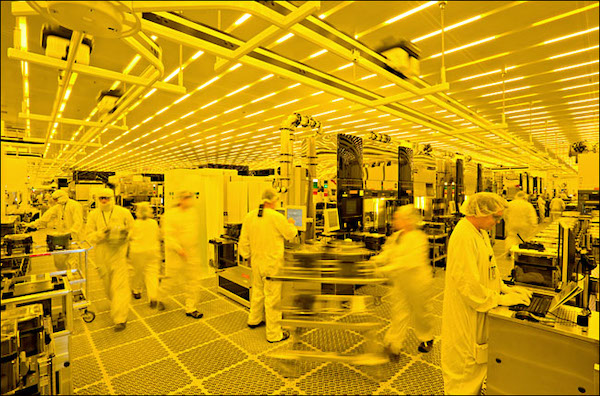
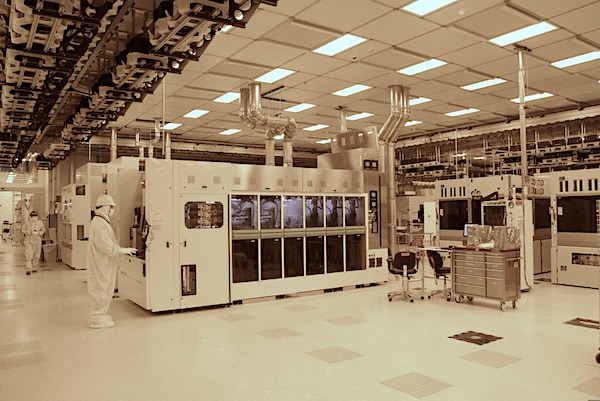
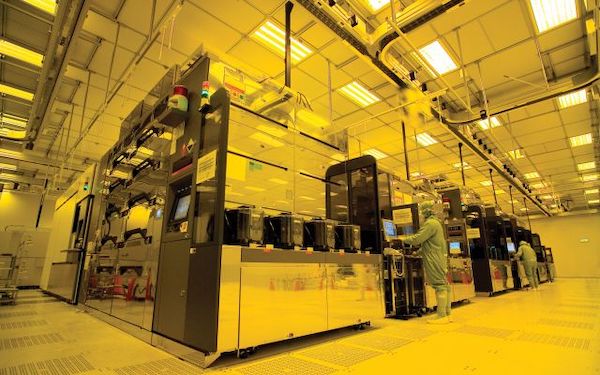
Semiconductor & Electronics Fab
Air Pollution Control
Applications / Use Cases
Air pollution control applications include:
- Semiconductor fabricators
- Circuit board
- Electronics
- LCD displays
- Solar Panels
- Chip fab
- Battery manufacturing (Li-ion) - NMP recovery
- Computers, monitors, televisions
- Printed circuit boards (PCB)
- Soldering and coating processes
- Electronic components: transistors, capacitors, resistors, diodes.
- Silicon manufacturing
- Glass coating
- Wafer etching (microfabrication)
- Vapor deposition
Primary Contaminants
- VOCs - Volatile Organic Compounds
- HAPs - Hazardous Air Pollutants
- Odors
- Expensive solvents to recover
Types of Equipment Used
- Catalytic Oxidizer
- Regenerative Catalytic Oxidizer
- Thermal Oxidizer
- Regenerative Thermal Oxidizer
Key Challenges
Some of the key challenges in the semiconductor and electronics industry are:
- Fast-paced industry with process turnover, project speed is crucial
- Requiring 100% uptime for 24/7 operations
- Precision manufacturing down to the nano-meter scale
- Pressure-sensitive manufacturing process: the VOC abatement equipment cannot exert any back-pressure on the exhaust air flow when switching valves or transitioning
- High quality standards, high reliability required
- Acid compatibility and corrosion protective materials
- Strict, high standards for controls and PLCs
Recommended Suppliers
Recommended Suppliers with Industry Experience:
- Catalytic Products (CPI)
- Offers thermal oxidizers, catalytic oxidizers, concentrators, filtration systems, and heat exchangers. CPI has provided RTOs to Honda, Volkswagen, and more. Request a quote from Catalytic Products
How Much Should It Cost? Find a Supplier, Get a Quote.
Wastewater Treatment Pollution Control
Applications / Use Cases
Applications in the Wastewater treatment industry include:
- Wastewater treatment
- Sewage treatment
- Contaminated water
- Ground water remediation
- Industrial wastewater (IW)
- Oil & Gas, water recovery
- Superfund sites, pump and treat
- Municipal waste treatment
- Vent gas streams
- Storage tanks
Primary Contaminants
- Odors
- Hydrogen Sulfide (H2S)
- Dimethyl sulfide
- Methanethiol (Methyl mercaptan)
- Carbon disulfide
- Propanethiol (n-Propyl mercaptan)
- Ammonia
- Toxic substances
- Halogenated compounds (HF and HCl)
- Trichloroethylene (TCE)
- VOCs - Volatile Organic Compounds
- Diesel range organics (DRO)
- Gasoline range organics (GRO)
- HAPs - Hazardous Air Pollutants
Types of Equipment Used
- Aqueous RTO - can handle both liquid and gas-phase VOCs, mixed with water. The wastewater is sprayed into a hot air stream, turning it into vapor. It's then passed through the RTO in normal fashion.
- Regenerative Thermal Oxidizer - the 3-chamber RTO and Rotary RTO are the best solutions for odor abatement.
Key Challenges
The first challenge in wastewater treatment is fully separating the components using an air stripper, or chemical means of separation.
Another major challenge is odor control. Many odors can be detected at very low concentrations, often less than 1 part per million (<1ppm) or some compounds can even be detected into the parts per billion (ppb) range. Odor is tricky to control because it can be subjective to detect, sometimes judged by an odor panel. To remain in compliance, odor control systems, odor scrubbers, and oxidizer systems need to be engineered for 99+% destruction rates. A three-chamber RTO is needed.
Recommended Suppliers
Recommended Suppliers with Industry Experience:
- Catalytic Products (CPI)
- Offers thermal oxidizers, RTOs, and heat exchangers. CPI has provided RTOs to wastewater treatment applications. VANGUARD Ammonia Abatement System from CPI
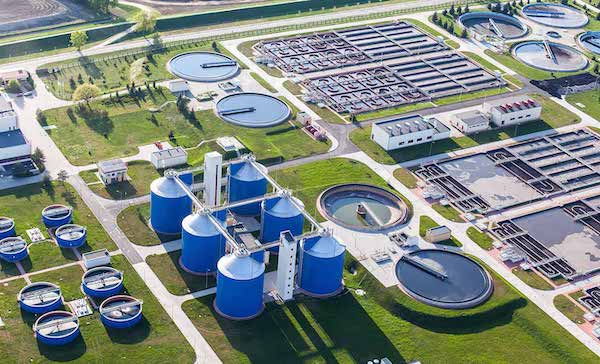
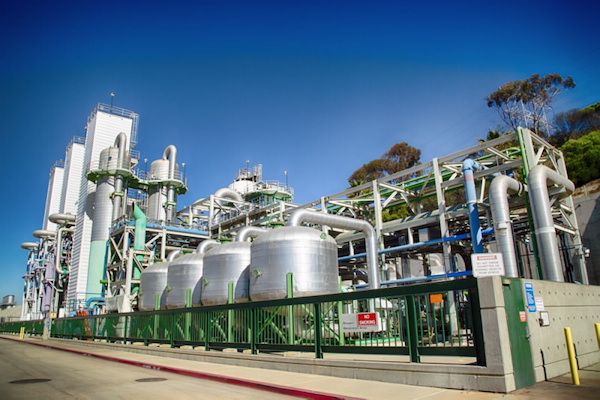

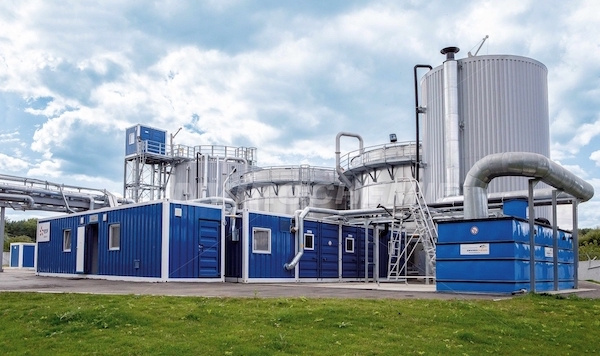